EHS Manager Q&A: How We’re Building A Culture of Safety
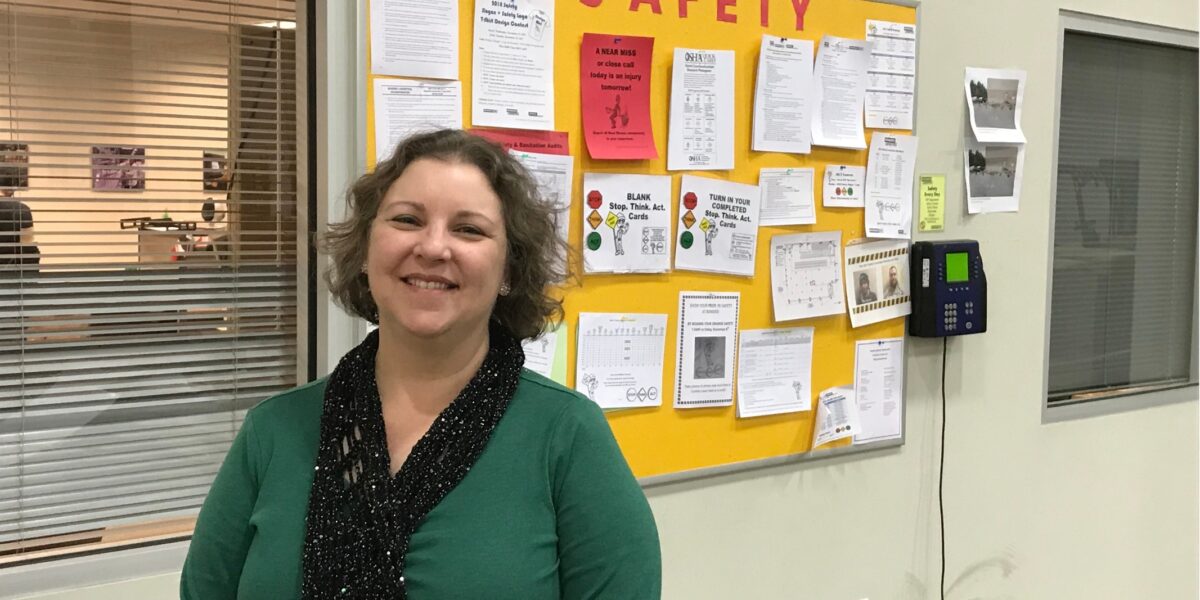
By Jan McCormick, Jr., Marketing Director
The importance of safety in logistics cannot be understated. With so many different facets of work we do, whether it involves forklifts, mass production, or hazardous materials, making sure the working environment is safe has to be a top priority. That can take a lot of effort, but if you make it part of the company culture it makes it much easier. That’s exactly what our Environmental Health & Safety (EHS) Manager Cynthia Lewis has been able to do since coming to Bonded in 2015. This Q&A outlines how communication, documentation, and a change in mindset are getting it done.
Tell us a little bit about your background.
I started my career in the Delaware State Fire Marshall Office holding many roles, including Technical Services and Acting Chief of Technical Services. After that I moved to DuPont where I lead the Safety, Health, and Environmental Communications and Activity Team. We managed and motivated a diverse workgroup to communicate safety messages and engage employees in safe work practices on and off the job. Before coming to Bonded, I worked as a Safety Specialist at Coty US. There I was responsible for ensuring compliance with OSHA and NC Department of Labor. We developed and implemented several sustainable systems for safety training, Process Safety Management, Behavior Based Safety System (BOSS) audits, incident investigations, and communication methods.
What were some of your first priorities after joining Bonded?
Bonded already had a safety culture when I came aboard, so I had a baseline that I could build upon. I spent the first 30 days assessing. I implemented Six Sigma, observed things, put them into categories, and then presented to key executives initiatives on emergency preparedness, maintenance, capital projects, etc. We established priorities for each area, and that helped us start attacking what was important. Documenting was also a top priority. Some of our clients were auditing us and safety is a big part of it, such as security and risk assessment. I also created monthly topics on things like safe lifting and fire prevention. I do training updates and track the number of training sessions. The first year we documented training 1,201 times and we are up to 6,641 times this year.
Can you give some examples of how you communicate safety?
When I started, Bonded’s safety committee was pretty static. I made it more active by having them establish Safety Boards and deciding as a group what they wanted the boards and information to look like. Each year I added more responsibilities like conducting weekly eye wash/safety shower inspections, monthly fire extinguisher and spill kit inspections, assisting with monthly audits, and leading a tailgate topic once a week. This year, they are taking turns leading the Safety Committee Meetings including developing the agenda, taking minutes, and time keeping during the meetings. I worked with management to put in term limits to get more employees involved, keep them engaged, and identify those employees that we can develop into the future safety leaders of the company. I also started a meeting with Facility and General Managers to discuss what’s going on at higher level. I let them know what safety committee members are working on, what they are looking for, and try to get everyone’s feedback. It’s a good way to network internally and share experiences. I also do weekly emails to let all FM’s know what’s going on with incidents at different facilities. Being transparent and showing everyone every incident helps so they can learn from other’s mistakes.
Talk about some of your big safety wins.
Instituting behavioral observation audits is a big one. It’s where you train people on what safe behavior looks like, such as are they lifting safely, are they operating a forklift safely. If you get those unsafe acts reduced, you are going to have less near misses, and that means less incidents. Preventative actions are another, where I established a root cause handout that everybody has to go over when there is an incident, even witnesses. And it’s not just for human instances, but also physical and systematic. I want them to think about job layout, equipment, is it anything that Bonded owns that could be changed or fixed. Gladhand locks have been a recent big win to keep trucks from driving away from our buildings before we’re ready.
How have the employees embraced this culture of safety?
Buy-in from employees has been very good and they appreciate having a safety culture in place. Sometimes you have to convince people that know the culture, but don’t necessarily want to abide by it. They want to cut corners to speed up the work that has to get done. And it takes time; it’s a constant journey with changes all the time. It’s not flip-a-switch. And it’s not just convincing the warehouse workers, but folks in the offices as well. Those folks can get hurt and training them on safety initiatives helps. And when warehouse workers see executive getting trained, then they are going to find ways to make time for it.
How about our customers?
I believe our customers are very happy to see the safety culture that we’ve got. Most of the big companies get it. They get that no one wants an employee hurt, even first aid. But they also look at if from the business side and say it’s just not good business to have an unsafe workplace.
What are some initiatives you are working on now?
I would like to get to the point where I can focus on e-learning, rolling out training modules to catch people at their desks and have them work for 15 minutes to get some training done. Feedback is also extremely important. We started doing employee pulse surveys on the corporate level, and safety is a part of it. I’d like to be able to work on a safety specific survey. I could take the results to the safety committee to see what we need to work on, discuss how we’re going to make changes.
What would you recommend to others who want to build a culture of safety?
First thing is recognizing you have a safety culture, whether good or bad, and establish a baseline. You have to assess the needs, prioritize them, and get to work. It’s also important to recognize it’s a journey and not a destination because even after you get to the point where all your policies are written, you have to sustain it, which is the hardest part of it. Following Six Sigma, five-s, or whatever lean approach, it’s going to be a struggle but you have to keep it going.
Interested in learning how our safety culture can improve your supply chain logistics? Contact us today!