Five Focus Areas for Onboarding Packaging Clients
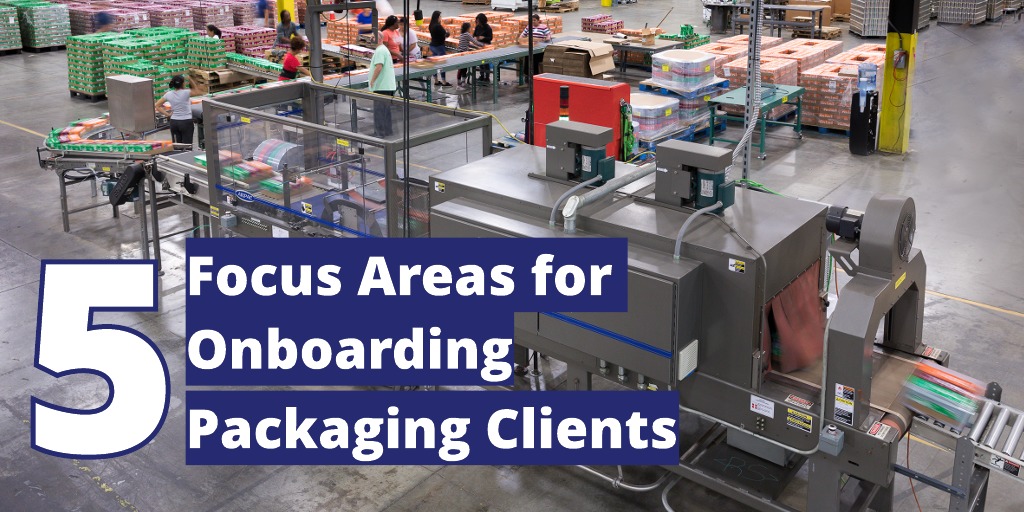
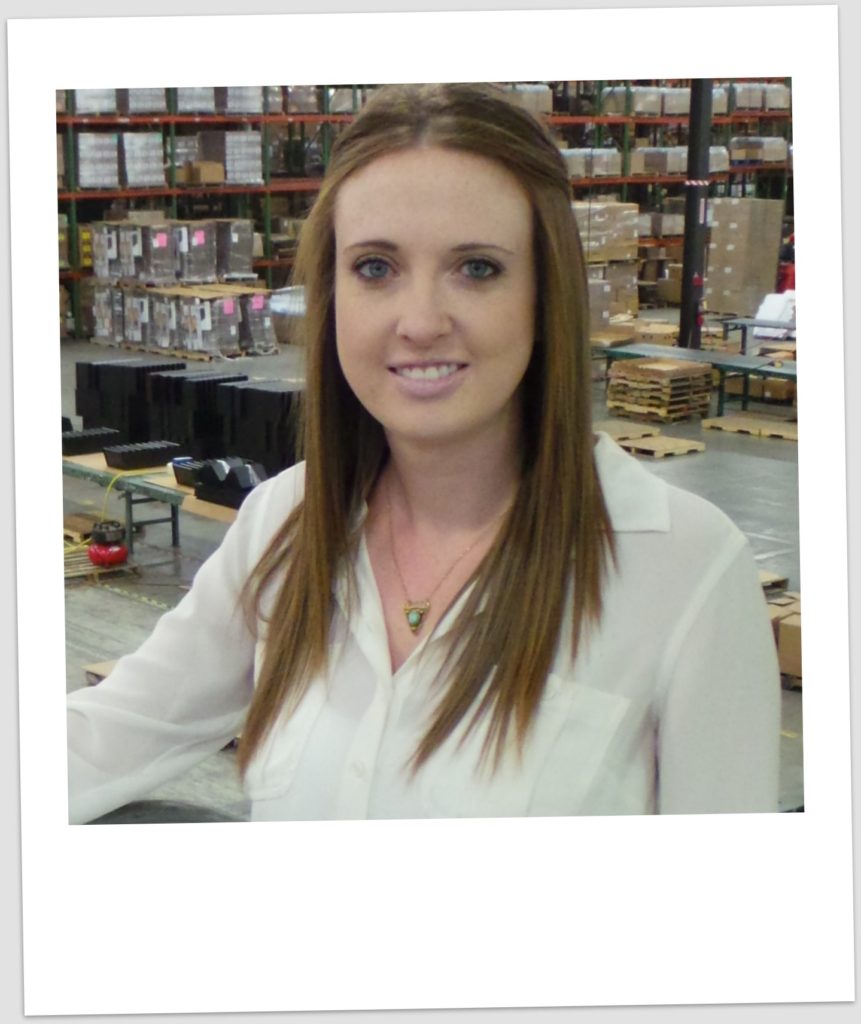
By Kara Jesse, Senior Manager of Project Development at Bonded Pac
We all know how important onboarding, the process of bringing on new clients or projects, is to business success. As a co-packer, clients come to us with all different kinds of projects. Sometimes it’s a one-time project, other times it could be on-going work that involves moving existing product and services into our facility. Each has to be handled in a different and unique way.
Our onboarding process starts with getting to know the client and identifying their specific needs. In some cases, we may have to adapt to what they need based on an established system. With others, we are creating a whole new system for them. In both situations, we always focus on these five areas: point of contact, systems set-up, quality standards, first article, and retailer requirements.
Point of Contact
The first thing we do during onboarding is assign each client with a single point-of contact, a Project Manager. The Project Manager will work with the client to establish a project timeline based on material availability and project due dates. They handle everything from tracking product arrival to ensuring finished goods are produced and shipped out on time. Most importantly, the Project Manager is responsible for one-to-one communication with the client, making sure they are kept up-to-date with what’s going on throughout the entire project.
Systems Set-up
Our packaging software from Nulogy assists in making the systems set-up as easy as possible. Project Managers are able to utilize the same part numbers our clients use, which helps to alleviate communication issues. Product is tracked from receipt, through production and shipping to allow full traceability. We also set our clients up with access to our web-portal, which provides them with real-time visibility of their inventory as well as several reporting features to track receipts and shipments.
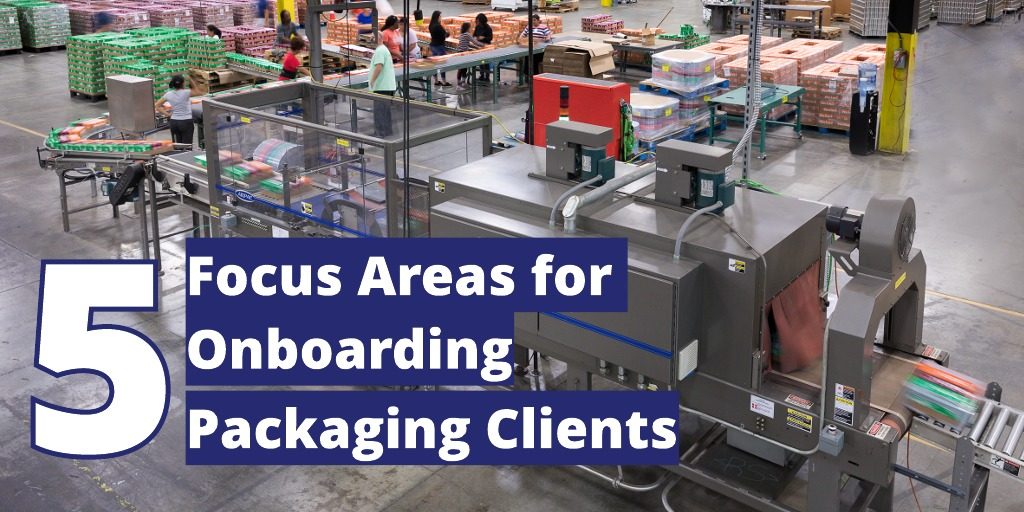
Quality Systems
It’s imperative to know ahead of time what quality standards are expected from the client and that they are clearly defined. We see ourselves as an extension of our client’s business, so we do everything we can to meet or exceed quality expectations. We rely on close communication to set-up quality standards and checks before we get started on any project. We have even established a quality system that enables us to mirror our client’s specific needs and ensure success.
First Article
A lot of times we are the eyes for our clients, so we always make sure to put together a first article for every project. The first article is a document that the Project Manager creates that includes a copy of the bill of materials, label formats, pictures of the finished good, and stacking diagrams. We tailor each first article to meet the needs of the client, and do not begin production until the document has been signed off and approved by the client. The first article is then uploaded into our system for reference by our production and quality teams throughout production.
Retailer Requirements
Most retailers have a specific set of vendor compliance guidelines that must be followed. This can include pallet types, shipping labels, placard placement, display design, bill of ladings, etc. We understand and value our client’s relationships with their retailers, and work with them to ensure we meet the specific requirements they outline for us.
Interested in learning more about our onboarding process and how it can help make your next packaging project a success? Click here to start a conversation today with us!